El coche eléctrico se perfila como la alternativa a los vehículos de combustibles fósiles. Aunque la principal alternativa debe ser siempre el transporte público. Más eficiente pero no siempre suficientemente valorado ni cuidado. El caso es que para que el automóvil eléctrico sea más sostenible que su antecesor, debe ser capaz de corregir los errores del primero. Es decir, no basta con abandonar el petróleo como combustible. También hace falta reducir su impacto ambiental. Y esto pasa por recuperar los materiales empleados en su fabricación. Por ejemplo, con plantas de reciclaje de baterías capaces de darles una segunda vida.
A medida que el parque de coches eléctricos envejece, su vida útil se reduce. Y llega un momento en el que hay que cambiarlos por otro modelo o cambiar sus baterías. Con anterioridad, hemos visto que el reciclaje de baterías de automóviles eléctricos es un tema en el que debemos evitar errores del pasado. Existe la tecnología necesaria para el reciclado de las baterías, pero todavía es necesario investigar alternativas y procesos más eficientes y sostenibles. Precisamente, la sostenibilidad debe ser clave para asegurar que el futuro del coche eléctrico es acorde al futuro que queremos construir.
Sostenibilidad aparte, recuperar los materiales presentes en las baterías eléctricas también es una cuestión de reducción de costes para las empresas que fabrican baterías y automóviles eléctricos. Muchos de esos componentes son difíciles de encontrar. Y países como China, Corea del Sur, Japón o Estados Unidos, libran una competición por ver quién se hace con estas materias primas de importancia estratégica.
Así que, además de amasar grandes cantidades de litio y otros materiales, surge la necesidad de recuperar esos mismos materiales disponibles en viejas baterías. Un ejemplo es la recién inaugurada planta de reciclaje de baterías de Mercedes-Benz, el fabricante de automóviles de origen alemán. Una planta de última generación y que, entre sus características más destacadas, promete recuperar casi la totalidad de materiales de las baterías a reciclar.
Una planta de reciclaje de baterías de lo más eficiente
Mercedes-Benz tiene una planta de fabricación de vehículos en Kuppenheim, Alemania, desde 2009. En ella trabajan 956 empleados, según indica su propia página oficial. Esa planta, junto a las de Sindelfingen, Bremen, Hamburgo y Kecskemét, trabajan de manera coordinada. Cada una con sus propias funciones. La de Kuppenheim, en particular, “fabrica componentes de carrocería, partes estructurales y de la carrocería, principalmente para vehículos compactos Mercedes-Benz”. Y desde no hace mucho, cerca de esta planta de fabricación hay otra instalación. Una planta de reciclaje de baterías. Libre de emisiones de CO2.
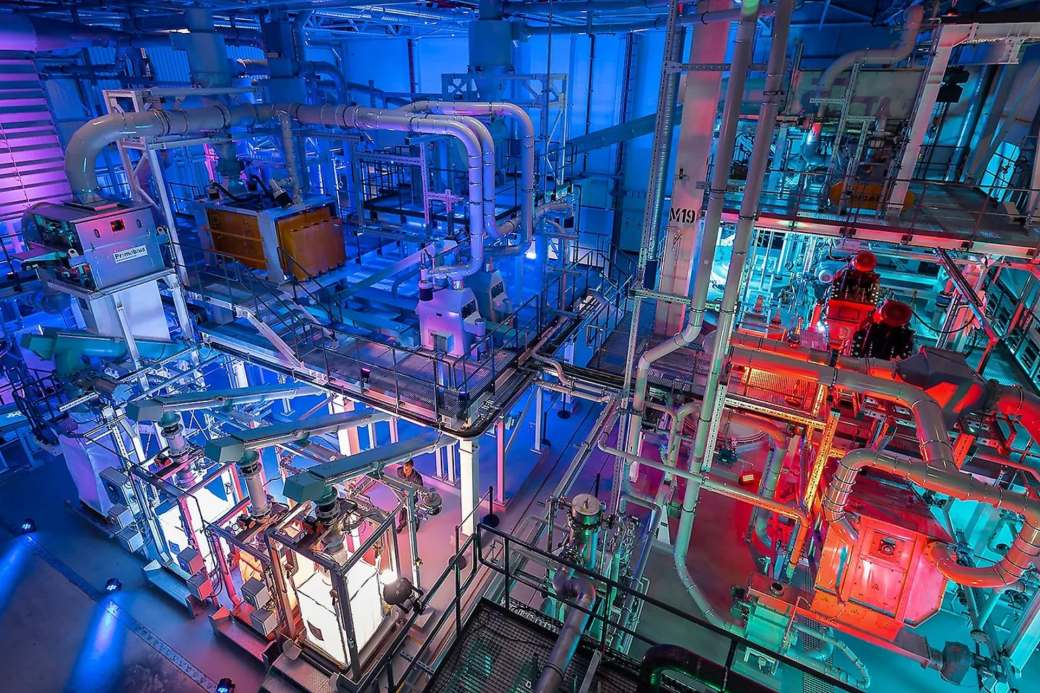
La inauguración oficial fue a finales de octubre de este año. Se trata de la “primera planta de reciclaje de baterías con un proceso mecánico-hidrometalúrgico integrado, lo que convierte a Mercedes-Benz en el primer fabricante de automóviles del mundo en disponer de un ciclo cerrado de reciclaje de baterías con su propia instalación interna”. Muy acorde con conceptos tan en boga hoy en día como la economía circular.
Para hacer posible esta planta de reciclaje de baterías, Mercedes-Benz ha trabajado mano a mano con Primobius, empresa especializada en reciclar baterías con procesos de bajas emisiones. Empresa que, a su vez, es una joint venture entre la compañía australiana Neometals y el grupo alemán SMS Group. Por lo demás, aunque esta planta ha supuesto una gran inversión para el gigante automovilístico, esa inversión le será devuelta al ahorrar en costes de transporte, compra y recuperación de los materiales de las baterías que pasarán por su planta de reciclaje. No solo eso. El proyecto también ha recibido fondos públicos de las autoridades alemanas. Y, según estimaciones, la planta será capaz de recuperar 2.500 toneladas de materiales cada año. El equivalente a 50.000 baterías eléctricas.
En qué consiste el reciclaje mecánico-hidrometalúrgico
Pero lo más llamativo de esta instalación de última generación es que, según sus responsables, “la tasa de recuperación esperada de la planta de reciclaje mecánico-hidrometalúrgico es de más del 96 por ciento. En esta planta de reciclaje de baterías se pueden recuperar materias primas valiosas y escasas como el litio, el níquel y el cobalto”. Así, una vez recuperados, estos materiales formarán parte de “nuevas baterías para futuros vehículos totalmente eléctricos”. Según Mercedes-Benz, sus instalaciones son las primeras en emplear este método en Europa. Un método que “cubre todos los pasos, desde la trituración de los módulos de la batería hasta el secado y el procesamiento de materiales activos de la batería”.
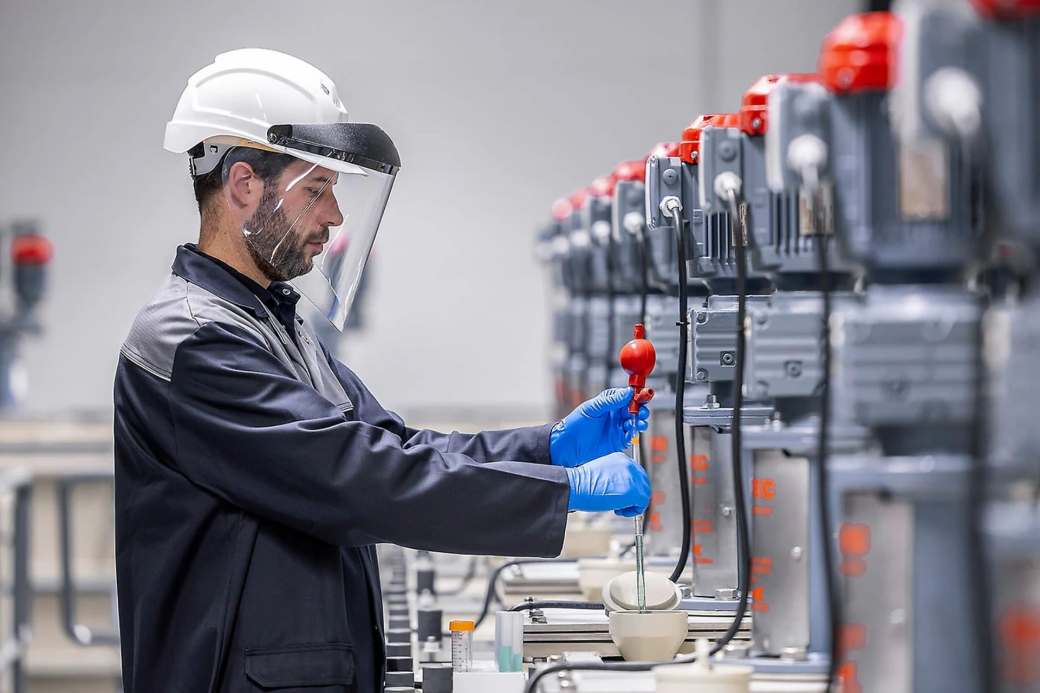
Primero, el proceso mecánico separa plásticos, cobre, aluminio y acero. Un proceso “complejo y que requiere varias fases”. A continuación, el proceso hidrometalúrgico se encarga de lo que se viene a llamar masa negra. Se trata de un polvo negro que se obtiene de triturar y separar los componentes de las baterías y demás chatarra. “Son los materiales activos que forman los electrodos de las celdas de la batería. Los valiosos metales cobalto, níquel y litio se extraen individualmente en un proceso químico de varias etapas”. Y esos materiales vuelven a la cadena de montaje. Para fabricar nuevas baterías.
El proceso hidrometalúrgico de la planta de reciclaje de baterías de Mercedes-Benz es menos intensivo en términos de consumo de energía y desperdicio de material. A diferencia del método pirometalúrgico, que es el más utilizado, hoy en día, en suelo europeo. Y en las instalaciones de Mercedes-Benz, al menor consumo de electricidad se le suma que la energía que utiliza proviene de fuentes renovables. “El área del techo del edificio de 6.800 metros cuadrados está equipada con un sistema fotovoltaico con una salida máxima de más de 350 kilovatios”.